Diols DCS Migration Phase 1 Manufacturing Newsletter Article
April 25, 2012
Diols DCS Migration Phase 1
The Geismar Diols Cluster was tasked with migrating to a new DCS system. This migration was necessary due to limited parts availability with the existing Novatech DCS system. After developing a User Requirements Specification (URS) and reviewing proposals from the five approved DCS Vendors, the ABB 800xA system was selected as the new DCS system for this Cluster. The project was broken into three phases to make the installation manageable while minimizing downtime associated with each conversion. Phase 1 of this installation was the conversion of the 1,4-Butanediol (BDO) Synthesis, Hydrogenation, and Distillation process units and was completed during the Geismar site Verbund. Phases 2 and 3 will convert the derivatives units (GBLI, GBLII, NMP, THF, and Poly THF) in 2012 and 2013.

It was quickly recognized that Phase 1 had to be completed during the February, 2012, Verbund turnaround to minimize the impact on the Geismar site. Failure to complete this project during this time would cause additional downtime for sites Verbund units (Acetylene, Diols, TDI, MDI, Aniline, and DNT). With KoS approval in March, 2011, the project team had less than a year to design, develop, plan, and implement Phase 1.
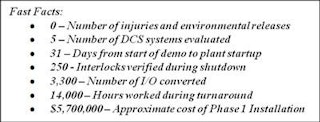
Early in the project, the Diols team interpreted the existing DCS databases for ABB to correctly implement control strategies. BASF also took responsibility for the design, layout of the I/O cabinets, improvement of under floor cable tray, and rearrangement of Marshalling panels. In addition, the team made preliminary reviews of graphics and replication of the Device blocks used for control of valves, pumps, and motors. Even with these efforts, a great deal of design and configuration work had to be completed during factory acceptance testing to make the DCS Interface operational. This was critically important no water runs would be completed at site during start-up activities.
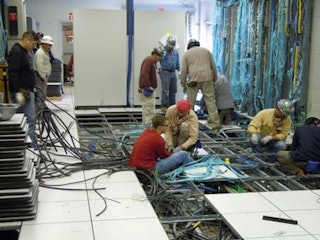
In addition to the challenge of converting the unit in this time frame, the team also had to develop contingency plans to support unit operations during the Phase 1 DCS outage. This included converting and moving over 180 I/O to a temporary Novatech controller while maintaining continuous operations. This I/O was used to monitor and control Synthesis reactor catalyst bed fluidization, run a hydrogen compressor for the Speciality Amines Cluster, and monitor and control tank farm operations to support the derivatives units (GBL, NMP, THF, and PolyTHF) during the Verbund. In addition, approximately 350 I/O were moved (without interrupting continuous operations) to the new ABB BDO Utilities controller in early February to run Utilities operations during the Verbund outage to support VTAR work and derivatives unit production.
Due to the time requirements, BASF, ABB, and MMR (installation/demo contractor) had several interactive planning sessions to ensure coordination of efforts. MMR did an excellent job planning activities during this shutdown. To minimize installation time, MMR pre-wired the signal wiring to the I/O cards in the DCS cabinets. Once the BDO units were shut down and secured, the old DCS system was de-energized and removed. The new ABB cabinets were set in place and wiring terminated. MMR completed their portion of the installation ahead of schedule. BASF performed loop checks for all field instruments to the DCS graphics to verify accuracy. Then BASF checked all DCS and SIS Interlocks to ensure that these interlocks would perform correctly when needed.
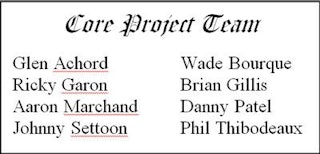
To make this transition as easy as possible for the Operators, new system tools such as interlock tables were implemented to show Operators the causes behind interlock trips. With similar functionality and knowledge of how to operate the production units, the Operators could concentrate on learning how to interface with the new DCS system. To gain this familiarity, Operators, Supervisors, and Instrument Technicians were key participants in training and factory acceptance testing. The operators were also deeply involved in loop and interlock checks. They also operated utilities equipment on the ABB system prior to and during the actual VTAR. These opportunities allowed the Operators to get comfortable with the new system prior to actual unit startup and suggest operability improvements.
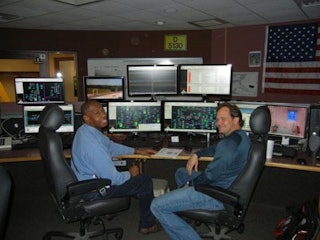
The successful installation of this project required a great deal of coordination and collaboration. In addition to maintaining the plant, the Diols Instrument team was deeply involved in design and checkout of the DCS System. Additional Instrument Technicians were brought in from the Geismar Amines unit, and from the Port Arthur and Freeport sites to support installation during VTAR. Finally, the project team was very responsive to the needs of the operating unit and made design changes as required during acceptance testing, installation, and start-up to ensure the plant would operate correctly. Phase 1 of the Diols DCS Migration was completed on schedule and within budget. Within two weeks of the startup of the BDO plant after the Verbund turnaround, a large export shipment was fulfilled.
Latest News
-
MMR Hosts Grand Opening for Regional Office in Salt Lake City, Utah
August 19, 2025 -
MMR Hosts Inaugural The Stars Ignite Event to Support Local Cancer Care
July 31, 2025 -
MMR Recognizes Spring 2025 Graduates
May 16, 2025 -
Continued Client Recognition for MMR Employees
March 13, 2025 -
MMR Celebrates Women in Construction Week 2025
March 12, 2025